Beyond the Balance Sheet: Unveiling the Real Price of Steel per kg
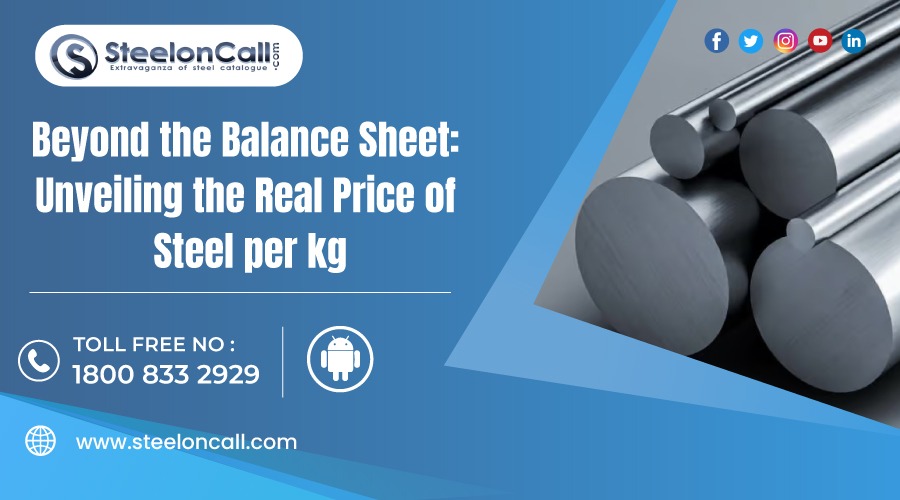
In the world of manufacturing and construction, steel is a foundational material that shapes the infrastructure we rely on daily. While the balance sheet reveals the monetary cost of steel, there are numerous hidden factors that contribute to the real price of steel per kg. In this article, we delve into these often-overlooked aspects, shedding light on the comprehensive picture of what goes into determining the true cost of steel.
1. Raw Material Sourcing and Quality:
1.1 Iron Ore and Coal:
The journey of steel begins with raw materials, primarily iron ore and coal. The geographical location of mines, geopolitical stability, and transportation costs all factor into the equation. High-quality ore and coal contribute to better steel quality, but these superior raw materials often come at a higher cost, impacting the final price of steel per kg.
1.2 Quality Standards:
Beyond sourcing, adherence to quality standards throughout the production process is crucial. Manufacturers investing in advanced technology and rigorous quality control measures may have a higher upfront cost, but the resulting premium quality steel justifies the expense.
2. Manufacturing Processes and Technology:
2.1 Production Efficiency:
The efficiency of manufacturing processes plays a significant role in determining the real price of steel per kg. Advanced technologies and streamlined production methods can enhance efficiency, reducing energy consumption and, consequently, the overall cost per kilogram.
2.2 Environmental Considerations:
As sustainability becomes a focal point, some manufacturers invest in eco-friendly technologies and processes. While these initiatives align with environmental responsibility, they may add an extra layer of cost to the steel production process.
3. Logistics and Transportation:
3.1 Global Supply Chain:
Steel is a globally traded commodity, and its price of steel per kg is influenced by logistics and transportation costs. Shipping, customs duties, and international trade dynamics contribute to the final cost per kilogram, making it imperative to consider the intricacies of the global supply chain.
3.2 Local Availability:
The proximity of steel manufacturing plants to construction sites also impacts the real price of steel per kg. Local availability can reduce transportation costs and provide a competitive edge in pricing.
4. Market Demand and Economic Conditions:
4.1 Market Fluctuations:
Demand for steel, as determined by economic conditions and market trends, plays a pivotal role in its price of steel per kg determination. When demand peaks occur, prices can increase while economic downturns could result in more reasonable pricing structures.
4.2 Currency Exchange Rates:
For global transactions, currency exchange rates come into play. Fluctuations in currency values can impact the real cost of steel per kilogram for both buyers and sellers engaged in international trade.
5. Regulatory Compliance and Certification:
5.1 Compliance Costs:
Stringent regulations governing the steel industry contribute to compliance costs. Manufacturers adhering to environmental, safety, and quality standards may incur additional expenses, reflecting in the final price of steel per kg.
5.2 Certification and Testing:
Acquiring certifications and conducting rigorous testing to ensure steel meets industry standards also adds to the overall cost. However, certified steel offers reliability and assurance of quality, justifying the associated expenses.
Why Maintain a Balance Sheet in the Price of Steel per Kg?
1. Financial Transparency and Accountability:
1.1 Cost Breakdown:
A balance sheet allows for a detailed breakdown of the costs involved in the production and acquisition of steel. This transparency is crucial for understanding where financial resources are allocated throughout the supply chain, from raw material sourcing to manufacturing processes.
1.2 Accountability in Spending:
By maintaining a balance sheet, businesses and manufacturers can be held accountable for their spending. It becomes clear how much is invested in raw materials, production efficiency, transportation, and compliance. This accountability fosters financial responsibility and strategic decision-making.
2. Evaluation of Production Efficiency:
2.1 Identifying Inefficiencies:
The balance sheet acts as a diagnostic tool, helping identify inefficiencies in the production process. If certain stages of steel production are disproportionately expensive, the balance sheet highlights areas that require optimization for improved cost-effectiveness.
2.2 Technological Investment:
Businesses can gauge the impact of technological investments on production efficiency through the balance sheet. Whether it's upgrading machinery or implementing advanced manufacturing processes, the balance sheet reflects how these investments contribute to overall costs
3. Market Competitiveness:
3.1 Understanding Price Competitiveness:
For businesses operating in a competitive market, maintaining a balance sheet is essential for understanding their price competitiveness. Knowing the costs involved in producing steel per kilogram enables businesses to set competitive yet sustainable prices.
3.2 Strategic Pricing Decisions:
Armed with information from the balance sheet, businesses can make strategic pricing decisions. This involves balancing the need for competitiveness with the imperative of covering costs and ensuring profitability, all of which are critical for long-term sustainability.
Conclusion:
The real price of steel per kg extends beyond what appears on the balance sheet. Raw material quality, manufacturing processes, logistics, market dynamics, and regulatory compliance collectively shape the comprehensive cost of steel. As consumers, builders, and manufacturers, understanding these underlying factors is crucial for making informed decisions. While the monetary aspect is significant, a holistic approach that considers quality, sustainability, and market dynamics is essential in determining the genuine value of steel in construction and manufacturing.
Steeloncall: Where Quality Meets Affordability:
Choose Steeloncall for the perfect balance of quality and cost-effectiveness. We provide the best steel solutions that meet your budget requirements without compromising on the high standards of our products.